Wajima
Technique: Wajima-nuri
Wajima, located in the Ishikawa prefecture, has traditionally been called oya-no-minato, which can be literally translated as parent port. Its seaport was key in trading with China and the Korean Peninsula, as a result it is widely believed that Wajima was entry point of traditional arts from China to Japan. Its climate is also optimal in drying lacquer, and Wajima is the home to abundant forests of cypress trees, which are key in lacquer production. The lacquer art creation process in Wajima has been polished with each generation, reaching a truly unique process, pursuing an utmost level of craftsmanship. There are more than 140 steps in the creation of what is now known as Wajima-nuri (Wajima lacquer art), all sustained by many tools, craftsmen and workshops.
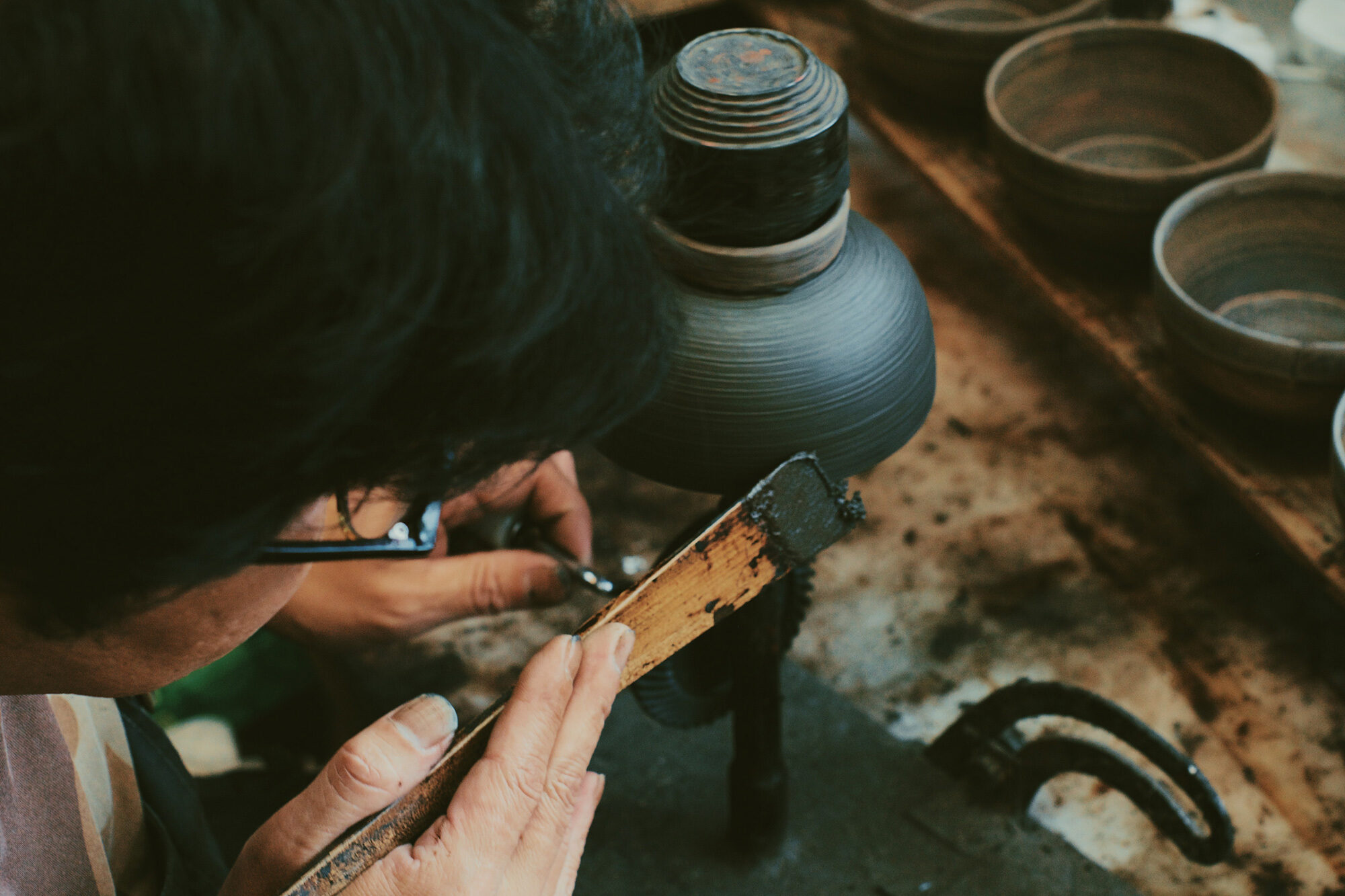
With the Japan Artisan Foundation, we have set foot on the Noto peninsula in Wajima to discover the unique appeal of wajima-nuri.
The beauty and preciseness of the wajima-nuri process truly overwhelmed us and allowed us to discover an artistic aspect not only in the final products, but also in the output resulting from each step.
However, the division of labour for each step also carries an amount of risks. The number of craftsmen and raw materials is gradually decreasing (a decrease that has been further accelerated with the COVID-19 pandemic), putting wajima-nuri on the brink of extinction. We decided that Wajima would be the first area where our organization would take action.
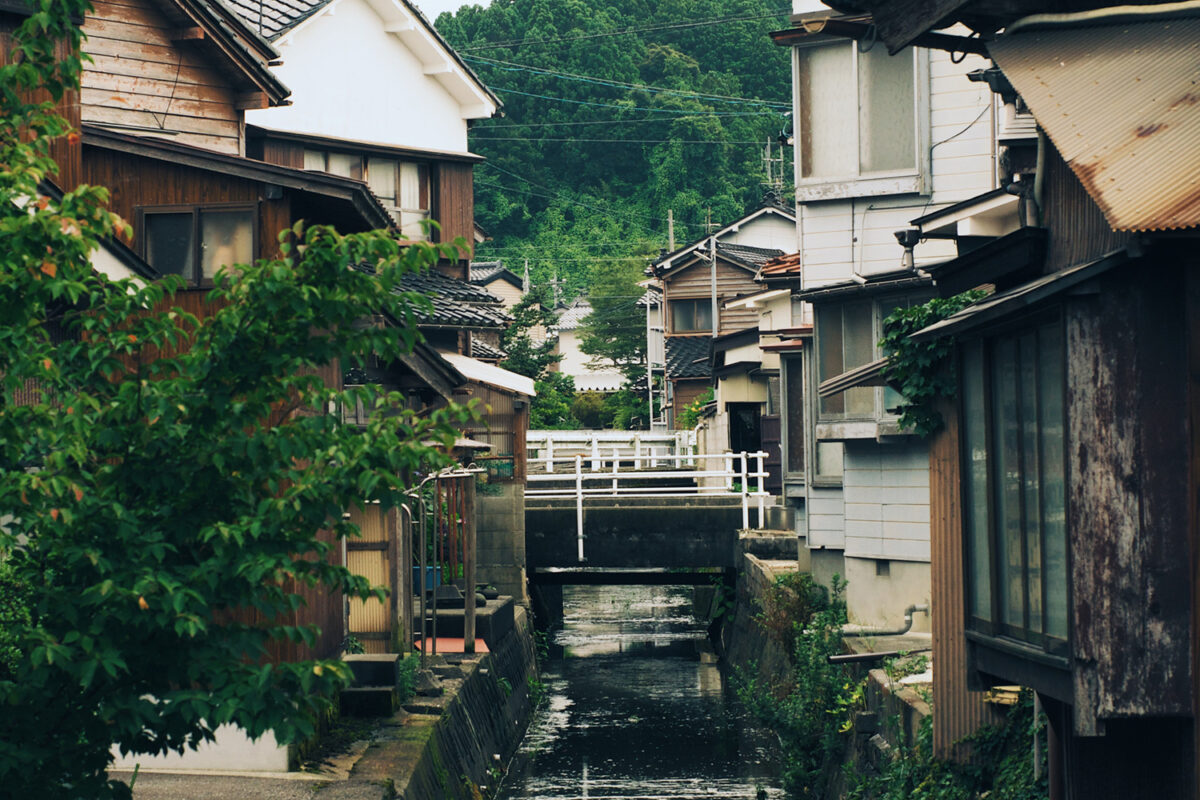
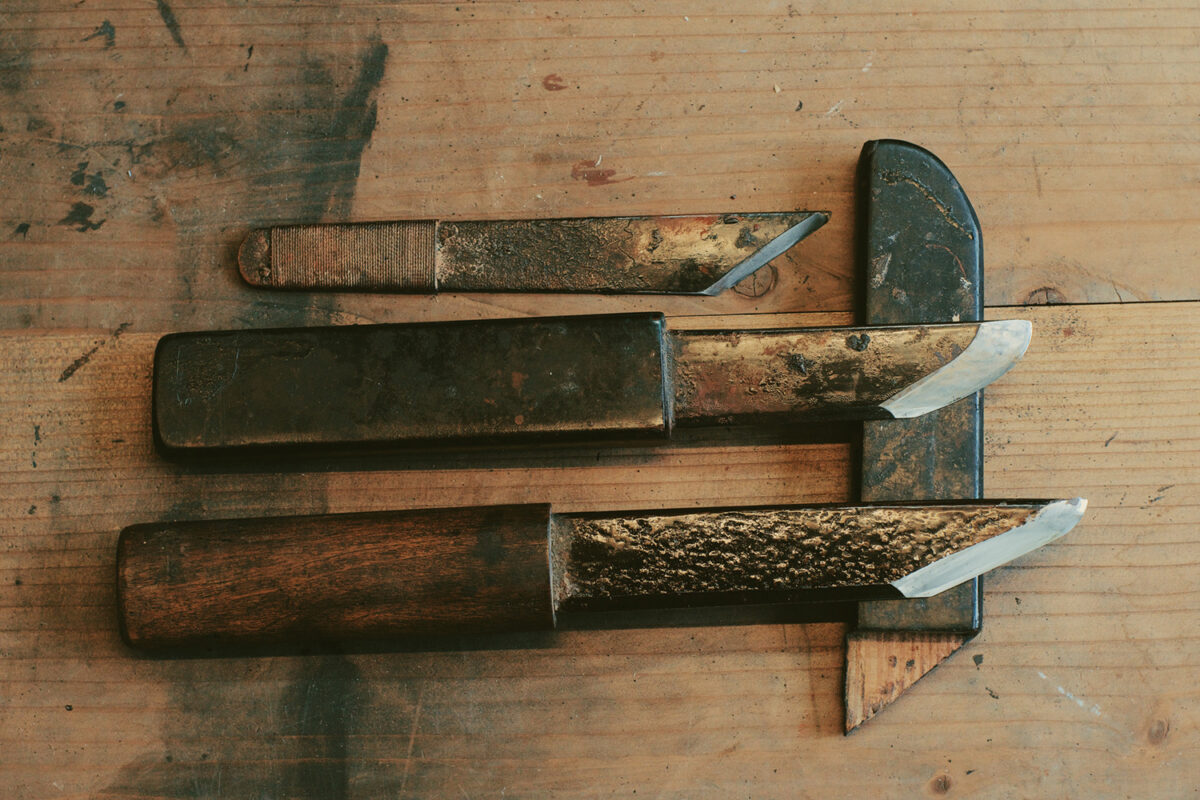
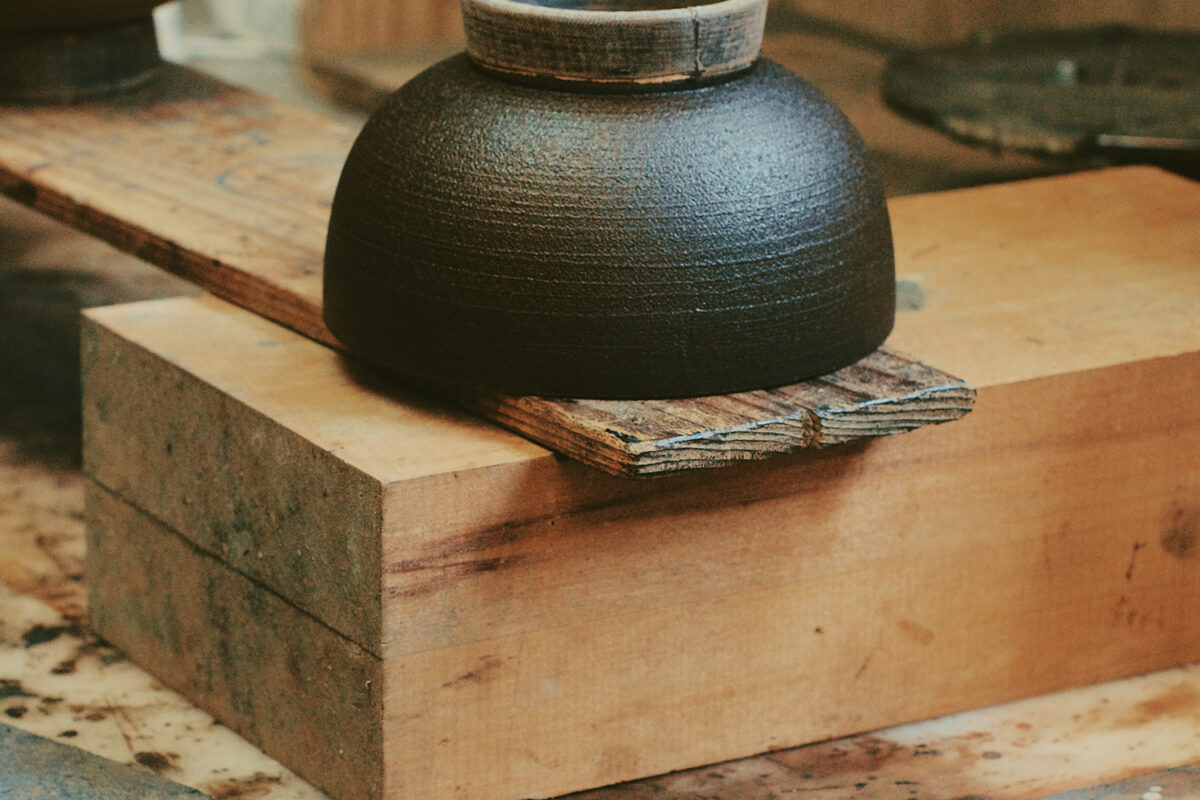
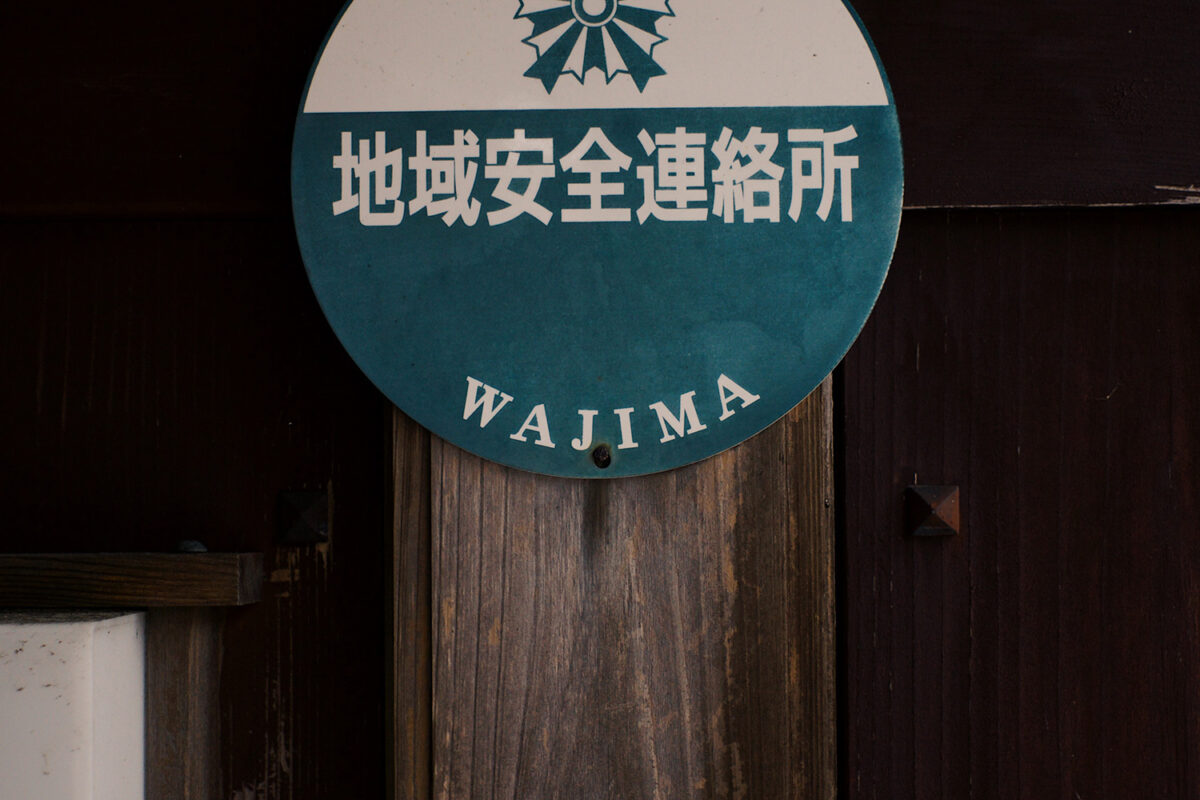
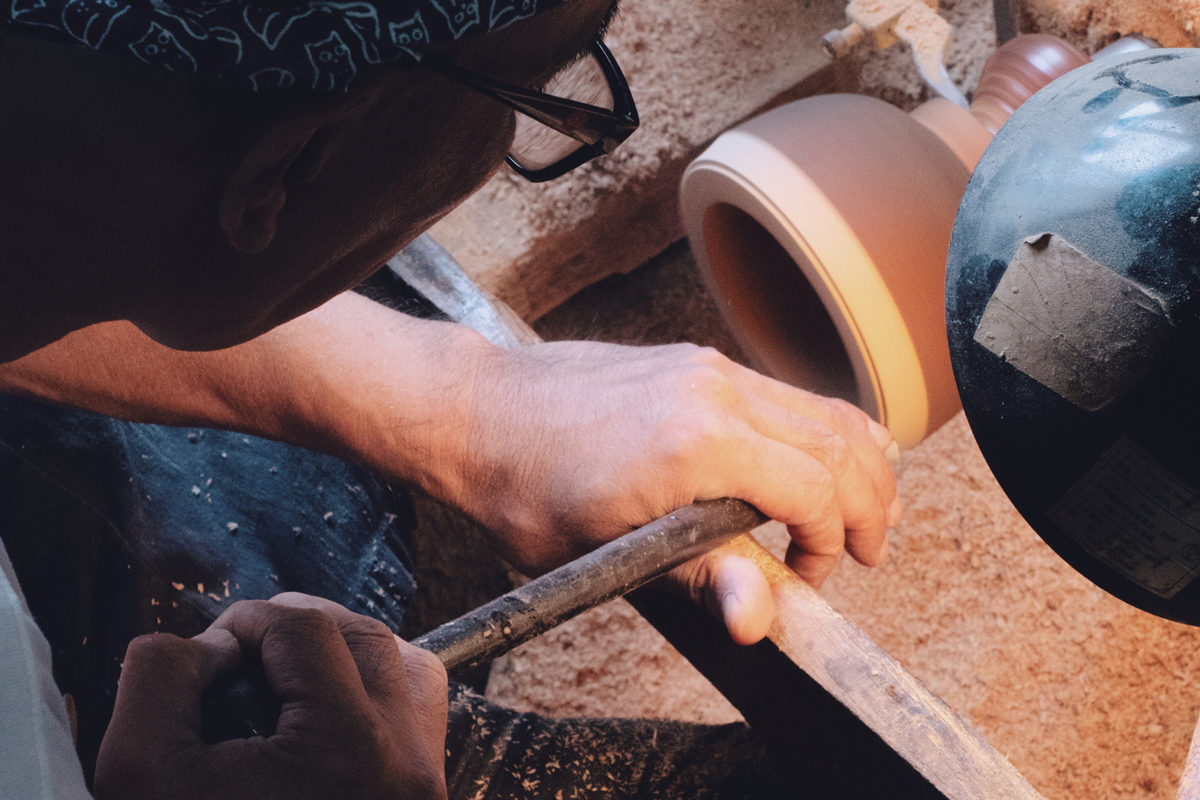
PROJECTS
Kaki Tree Project
On April 29, 2025, JAF held a tree-planting ceremony in cooperation with the "Revive Time: Kaki Tree Project" at Juzo Shrine in Wajima, which boasts 1,300 years of history. This project is an effort to spread the saplings grown from “A-bombed persimmon trees,” which miraculously survived the atomic bombing of Nagasaki, throughout the world as a symbol of peace.
SAKAZUKI
Originally, craft techniques have been applied to various manufacturing processes, cross-fertilized, and passed on while changing their forms from the time they were invented. The Wajima-nuri technique also has such a background. We contacted artist and art director YOSHIROTTEN to see if we could learn from this history and create something new by cross-breeding the craft with the sensibilities of today's artists.
YOIN
The Yoin speaker units were produced through a joint collaboration with EASTERN SOUND FACTORY (ESF). "Jinoko" used in Wajima base lacquer was blended with lacquer and then applied. This resulted in a chic, subdued appearance and improved sound quality.
GHOST LINKS
This project produced lacquer art works under the supervision of artist Charles Munka, who lives on Sado Island. After strolling around the town of Wajima and engaging in dialogue with many local craftspeople involved in Wajima lacquerware, Munka derived a lot of inspiration from Jidaiwan Taikan (1st Edition) (compiled by Gonroku Matsuda et al), which he discovered quite by chance, and thus he started the project.
YO-KOU
As the first step towards a series of projects about combining traditional crafts with cutting-edge technology, we created a glowing lacquered vessel called Yo-kou. The name is inspired by the idea of moonlight in the night sky shining in a cup of sake. Wajima Kirimoto, a lacquerware studio in Wajima-shi, partnered with NIPPON SHOKUBAI, a chemical manufacturing company headquartered in Osaka, to achieve that.
ARTICLES
Wankiji
This technique is for making circular vessels, such as bowls. Also called hikimonokiji (meaning “turned wood”), as the name suggests, the kiji is turned (hiki) by hand on a lathe by the kijishi using a variety of cutting tools.
Magemonokiji
This technique is for bending the boards into a circular or oblong shape to make the walls of a round dish or bento box, etc. The lumber used for material is called masameita (boards cut from the part near the center of the tree with a dense, straight grain) made from various types of cypress.
Sashimonokiji
As implied by the alternative name kakumonokiji (meaning square kiji), this is a technique for assembling boards to make square objects like nesting boxes, inkstone cases, square trays, and serving trays.
Hou-kiji
This technique is for woodwork with complex shapes and many curved surfaces, such as cabriole legs, lipped bowls, Buddhist altar fittings, and spoons. Its name comes from its extensive use of magnolia wood, which has moderate hardness and workability, and it is also known as kurimono-kiji, from the carving technique employed.
Shitaji-nuri (Undercoat)
The process of undercoating, which shapes the wood and reinforces vulnerable areas to create a solid and dense lacquered surface, is the essential step underlying its robustness. One of the main characteristics of this process is the use of techniques unique to Wajima-nuri such as nuno-kise and hon-kataji.
Togimono (Polishing)
This is the process of leveling the uneven surface left behind by the coating for a more beautiful finish. Polishing also creates microscopic scratches, where the lacquer seeps in, enhancing the adhesion between the wood and the lacquer.
Uwa-nuri (Top coat)
This is the final step of the lacquering process.High-quality lacquer of high purity (repeatedly filtered) is painstakingly applied. It is a technique that requires delicacy, care, and above all, a high level of lacquering skill.
Roiro
Roiro is a technique incorporated to further polish the finished upper lacquer surface to give it a polished gloss like a mirror surface. Quality charcoal finishing and even fingers and sebum of the craftsmen are used as tools to complete the lacquerware without even the slightest scratches.
Makie
In the Makie technique, pictures and patterns are brush-painted onto the lacquerware surface using lacquer. Next, metal powder, such as gold and silver, is sprinkled onto it to settle. Lacquer is then coated over the patterns and polished.
Chinkin
Chinkin is a decorative technique where you engrave patterns and drawing using a chisel on lacquerware after the final coating, then inserting gold and silver leaf/powder into the engraved groove.