ARTICLES
Shitaji-nuri (Undercoat)
The Wajima-nuri wrapping paper has a stamp with a seal reading "Dai-gokujo Nuno-kise Hon-kataji" to indicate its quality. The process of undercoating, which shapes the wood and reinforces vulnerable areas to create a solid and dense lacquered surface, is the essential step underlying its robustness. One of the main characteristics of this process is the use of techniques unique to Wajima-nuri such as nuno-kise and hon-kataji.
Process Overview
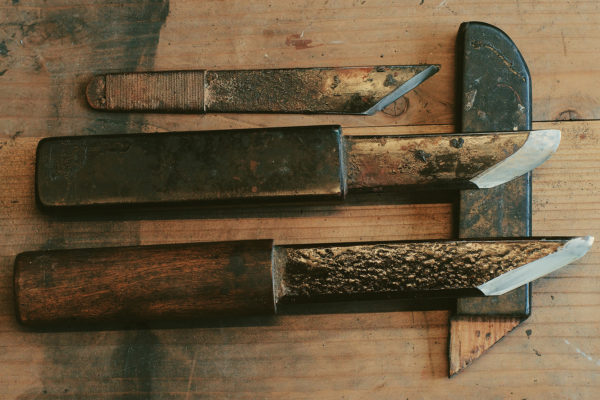
1 Kiji-gatame
The woodworker shallowly carves the joints and cracks in the wood with a craft knife and fills in the unevenness of the wood with kokuso (raw lacquer mixed with rice glue and zelkova wood meal). Next, raw lacquer is soaked throughout the wood to reduce deformation and water absorption (decay). After the woodworker applies the lacquer, a water-repellent film forms on the surface. The woodworker then polishes the surface with a sharkskin-lined board or sandpaper. This step enhances the adhesion between the wood and the lacquer applied in the next step.
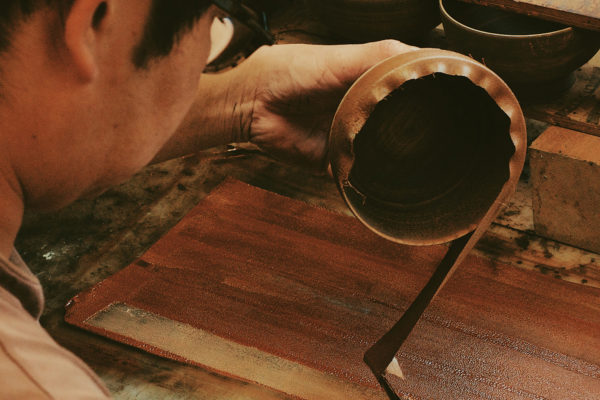
2 Nuno-kise
Linen cloth or cotton cloth is attached to the thin and fragile parts of the wood, such as joints, edges, and platforms, using kisemono-urushi (a mixture of raw lacquer and rice glue). After drying, the overlapping parts of the cloth are shaved with a craft knife to flatten them, and Somi-urushi (a mixture of raw lacquer, rice glue, and wood meal made from carbonized zelkova wood) is applied to remove the bumps between the cloth and wood. Finally, kara-togi (dry polishing) is performed with a rough grindstone to smooth the surface.
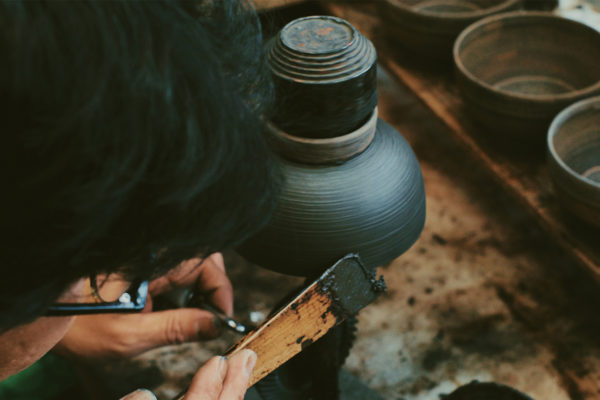
3 Ji-nuri
The woodworker applies an undercoat of raw lacquer mixed with rice glue and earth powder, with a spatula, in three stages: ippen-jizuke, nihen-jizuke, and sanpen-jizuke, and in between the three stages, dry-polishes the surface. The lacquer used in each stage gradually contains less rice glue, and the earth powder used in the undercoat gets finer. This increases the adhesion and hardness of the lacquer and wood. After sanpen-jizuke is finished, the polishing process begins.
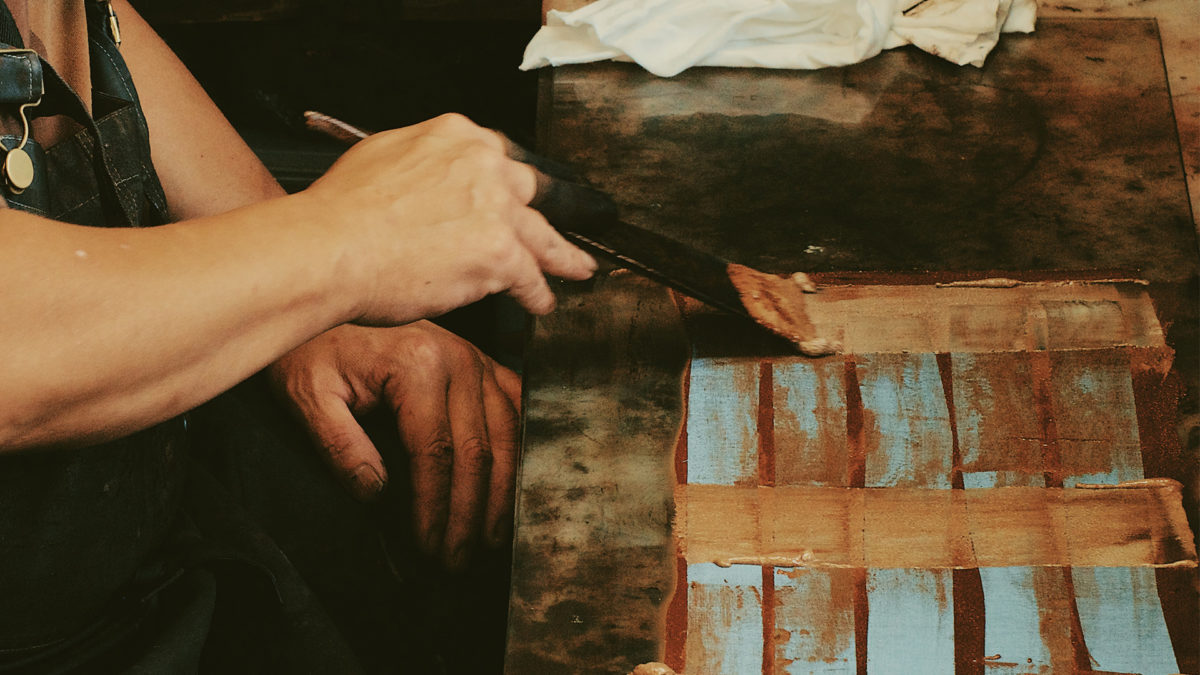
[Distinctive Techniques]
Nuno-kise: This is a technique for attaching linen cloth or coarse cotton cloth, called kanrei-sha, to thin and fragile wood areas such as joints, edges, and platforms. Rubbing the cloth hard with a spatula or fingertips allows it to adhere completely to the wood, increasing the strength and durability of the wood. The cloth also protects the wood if the lacquer surface peels or chips after use and prevents moisture from seeping into the wood from the damaged area.
Hon-kataji: This is a technique in which unique diatomaceous earth called jinoko (earth powder), which is mined only in Wajima City, is steamed and baked, then powdered and mixed with lacquer for undercoating. The jinoko, which has the same main composition as glass, has countless microscopic pores, and the lacquer penetrates these pores to create a solid undercoat. While gradually using finer jinko, repeatedly coating and grinding achieve unparalleled strength in the final product.
[Tools]
Cutting board (workbench), yume-dana, lacquerer's knife, uchi-kanna , naka-ganna, soto-ganna, yuka-ganna, spatula, brush, grinding wheel, rough grinding stone, ground grinding stone, water-resistant polishing paper, etc.
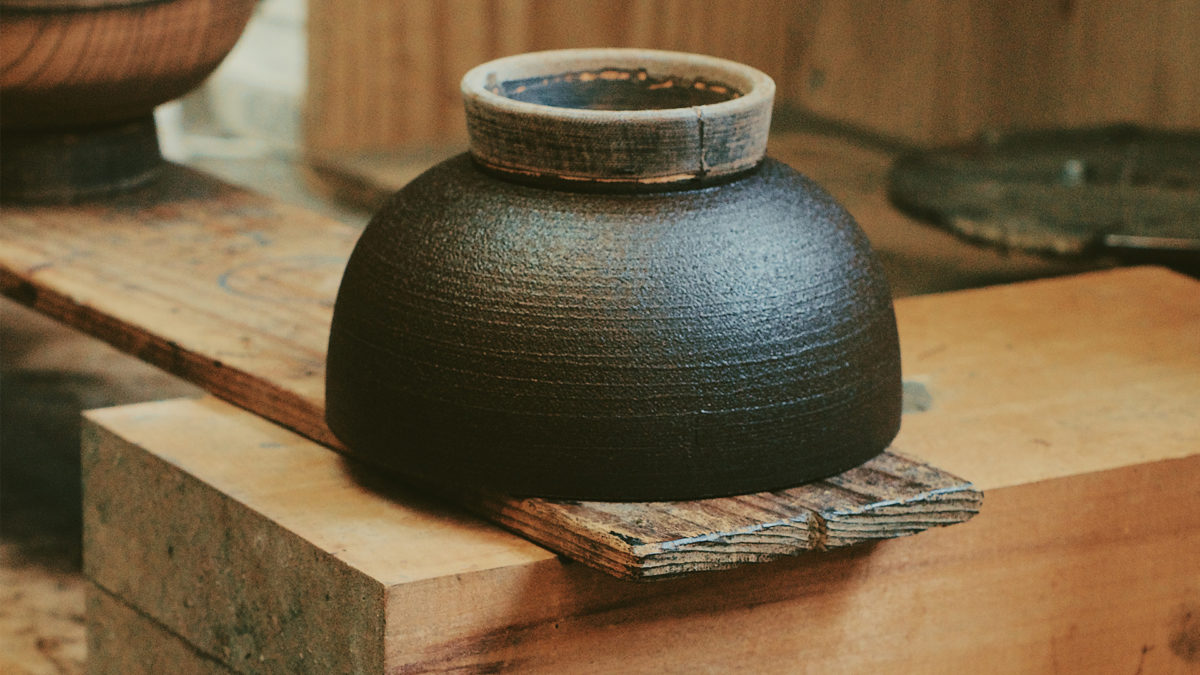
[Features and Use of Techniques]
The undercoat plays a vital role in "erasing" the wood beneath and creating the robustness with which Wajima-nuri is synonymous. Covering the wood grain with cloth and applying undercoat layers ensures there is no visible trace of wood on the finished piece.
In the traditional Wajima-nuri process, the undercoat serves only as a base for the top coat or decorations (roiro, makie, and chinkin). It does not serve to enhance the top coat's appearance.
However, at each stage of the elegant undercoat process, which consists of more than a dozen steps, the wood shows many expressions: at one stage, the wood grain is still visible; at another, the cloth covering the edges of the wood is still visible, and at another, the surface is still rough with jinko (earth powder). The differences in texture, color, and feel of these preliminary steps are unique enough to strongly inspire the creator's imagination.
Takaho Shoji, who works as a lacquerer at Wajima Kirimoto, a company that has produced and sold lacquerware in Wajima City for more than 200 years, is one of the people fascinated by the expressive possibilities of the undercoat. He has worked on about three dozen different undercoat application techniques, all of which are archived on a panel.
These are some examples: ① An applied technique of maki-ji, in which wood is covered with cloth and undercoated, then the surface is coated again after using earth powder. ② A technique of applying the ikkan-nuri method, in which washi paper is crumpled up and spread over the wood and then pasted with lacquer using a brush. ③ A technique in which the lacquerer makes a pattern on the wood surface by applying oil that does not mix with the lacquer and then finishes the coat using fuki-urushi (a technique of wiping off the lacquer with a cloth before it dries) with red lacquer. ④ A technique in which the lacquerer creates a pattern on the undercoated surface using a roller, etc.
Although many of these techniques are for practical designs such as tiles, walls, and other building materials, the uniqueness, variety, and beauty of these techniques make it seem like a waste of potential to limit their use to only building materials.
We can look forward to these craftsmen creating new products that take advantage of each technique's characteristic and using these in construction.