ARTICLES
Sashimonokiji
As implied by the alternative name kakumonokiji (meaning square kiji), this is a technique for assembling boards to make square objects like nesting boxes, inkstone cases, square trays, and serving trays. The lumber used for material includes paulownia and different types of cypress.
Process Overview

1 Drying
The lumber is cut into a board shape based on the dimensions of the item, after which it allowed to dry naturally, first outdoors in a well-ventilated area exposed to sunlight for at least six months, then indoors for several months.

2 Kidori
Each part is cut out based on the dimensions of the item, taking the edge grain and cross grain into consideration.
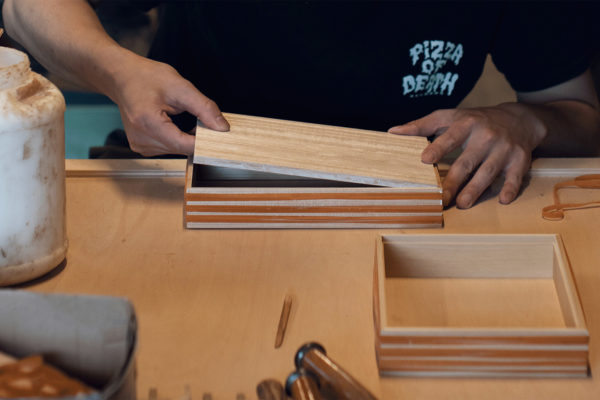
3 Assembly
After planing down the cut-out parts, the boards for each piece are assembled and glued together using wooden pegs and a mixture of raw lacquer, rice paste, and zelkova sawdust called kokuso. The glued parts can be easily separated, so they are fixed in place with twine or rubber bands, and allowed to dry naturally for 24 hours.
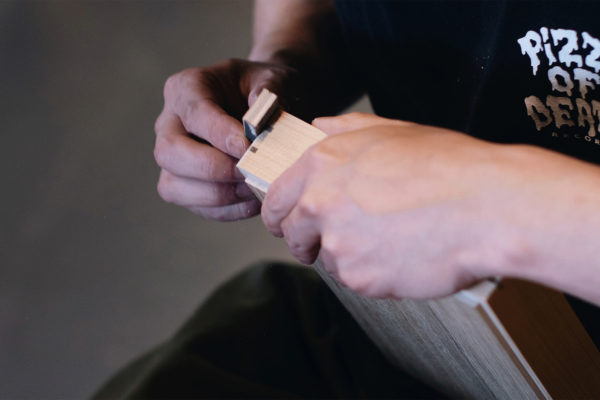
4 Tachikizuke
If the item has rounded outside corners, vertical boards are glued to the inside of the corners using kokuso. Once it has dried, the glued parts are cut down using a saw or other tool to create the rounded corners. Finally, they are planed to adjust the shape.
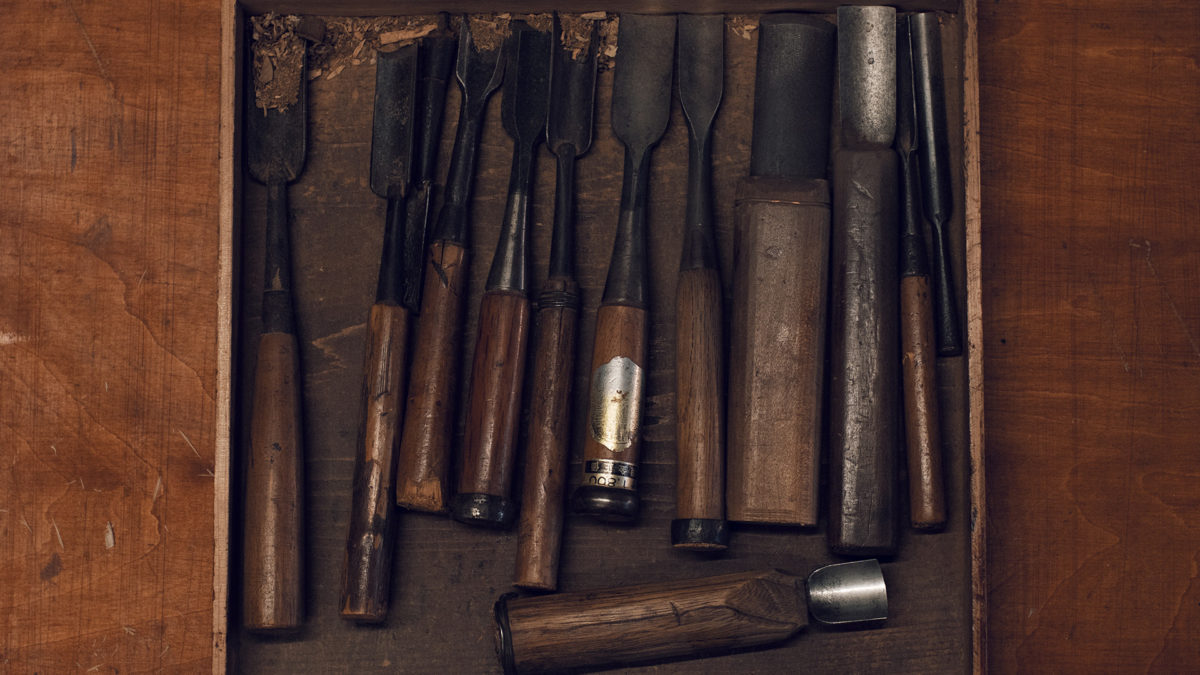
[Distinctive Techniques]
……
[Tools]
Saws, planes, chisels, line marking gauges, rulers, various guides for legs and tenons, etc., and woodworking machinery such as circular saws and power planers.
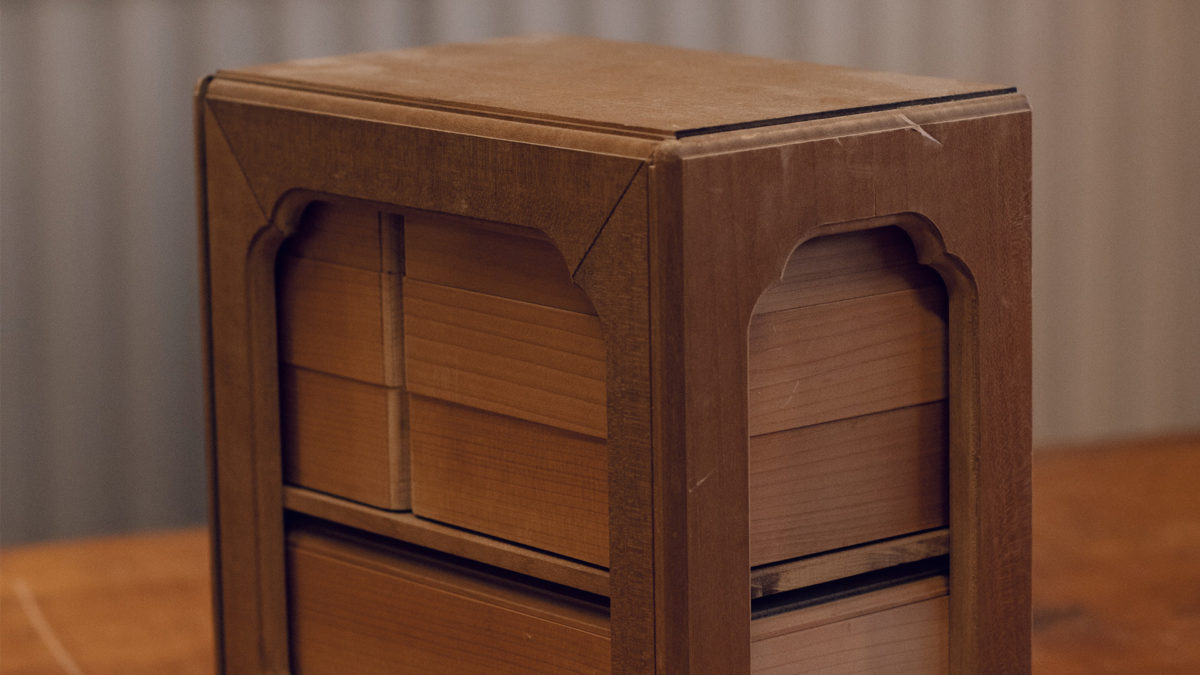
[Features and Use of Techniques]
Sashimono techniques can be used to assemble all kinds of square or rectangular household furnishings, from extremely small boxes only a few centimeters square to large furniture, all without using a single nail or metal fastener.
“You make clean right angles at each of the four corners, and insert the base board flush so there are no gaps. It’s very simple, and while it may sound easy, it’s actually quite difficult. Calling it basic may be somewhat misleading, but I believe that if you can't do sashimono, you’ll have a hard time with other kinds of work.”
Mr. Kubota is in charge of making kiji at Wajima Kirimoto, with 17 years in the trade after entering at the age of 23.
Like other kijishi, the job begins with cutting the wood.
“When I cut, I imagine how it will look when assembled, and think about what part of the wood will give the most beautiful finish. Next, the length, width, and thickness are planed down based on the dimensions of each part. The number one thing to keep in mind here is creating precise right angles to the flat surfaces. So, you need to make very precise adjustment to the tools you use as well.”
In addition to sashimono, Kubota also works on hokiji, which is covered in the next section.
“I created a dish called a “lotus leaf dish” out of a pure desire to make something new, if I might be so bold to say so. Everything from the design to the finish, I thought up by myself.”
At the same time, he does not neglect to look to things that have stood the test of time.
“Many of the shapes of kiji have been passed down since ancient times, but I think they can be redesigned and incorporated into new things. Many of the old things are appealing, including their names. Unfortunately, hardly any are being made today. The biggest obstacle to actually making them is the uncertainty about demand, but if they are simply left to languish that way, these good old things will no doubt end up being buried. I want to do something to change that.”
To rediscover things from the past and use them to create something new...
It seems clear that this is mindset of “revisiting to past to find the future” is worthwhile, and can translate to the application of these techniques as well.