ARTICLES
Magemonokiji
This technique is for bending the boards into a circular or oblong shape to make the walls of a round dish or bento box, etc. The lumber used for material is called masameita (boards cut from the part near the center of the tree with a dense, straight grain) made from various types of cypress. Other objects include hot water pots, containers for tea utensils or cooked rice, and square trays with rounded corners.
Process Overview

1 Warikoba
A piece of lumber is cut the required size is divided into quarters. It is then split to the required thickness along the grain using a hatchet, or cut into boards using an electric saw for thin pieces, then allowed to dry naturally outdoors for two to three months.
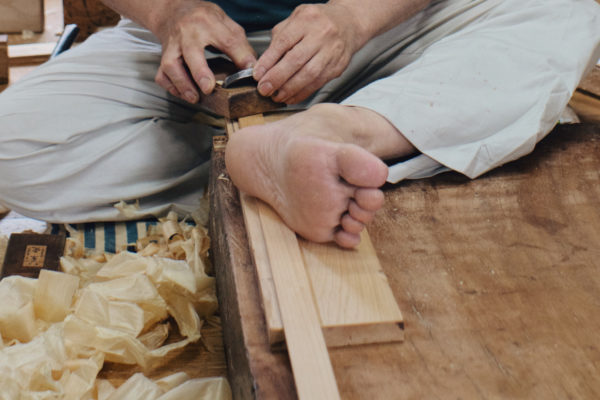
2 Soaking
The plank is soaked in water for roughly 24 hours, then allowed to dry naturally for several days. This makes the board flexible and easy to cut. Afterward, once the shape is adjusted by planing (nakashiage), both ends of the board are cut diagonally (awasemekezuri) so they can be bonded together, and it is soaked in water again for 24 hours to make the board more flexible and easily bent.
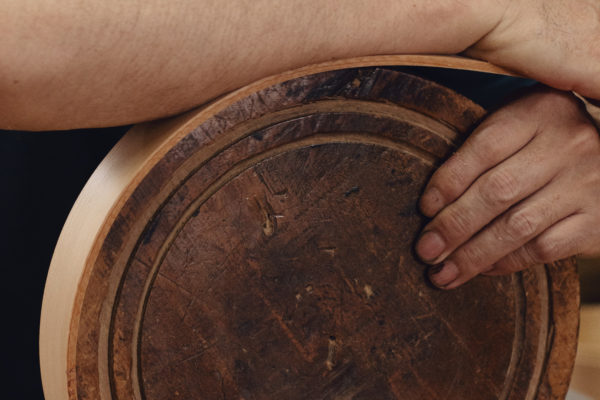
3 Mage
The soaked plank is bent around a wooden form (korogashi) made from a log. When bending it into an oblong shape like a square with rounded corners or an oval, a special bending form is made to bend it around. Next, the ends of the bent plank are overlapped and fixed in place with clamps and twine, then allowed to dry for several days. Afterward, lacquer, wood adhesive, or a mixture of the two called oshinori is applied to the overlapped parts with a spatula to bond it together, then allowed to dry for several days. Once it has dried, the thickness of the overlapped area is planed down to be uniform with the rest of the piece (doshiage).
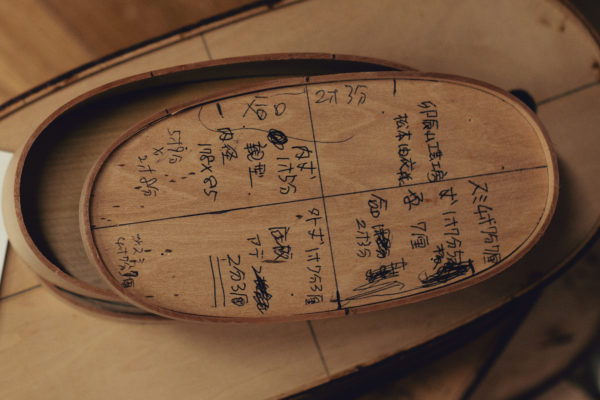
4 Teibanshiage
A base board cut slightly larger than the dimensions (teibankidori) is planed down and roughly finished (teiban nakashiage), then the shape is cut out with a saw based on a pattern for the base board. The cut edges are planed down and finished to a clean circle or curve to match the pattern.
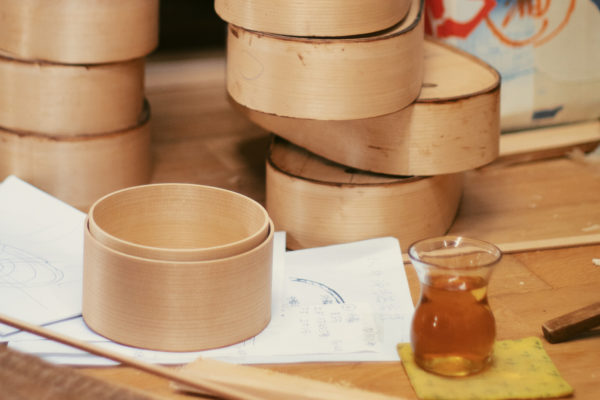
5 Soshiage
After attaching the bent board to the base board, the bottom or upper rim is planed down to adjust the height. Finally, the diameter of the upper rim is measured with a ruler, and if there is any warping, the artisan corrects it by hand.

[Distinctive Techniques]
Mage……A technique using the characteristics of wood to bend it into a circle or other shapes.
[Tools]
Saws, planes, a hatchet for warikoba, a circumference gauge called a shakujo, a bending form called a korogashi, pruning shears (vines from the moonseed plant are used as twine for holding parts in place), woodworking machinery, etc.
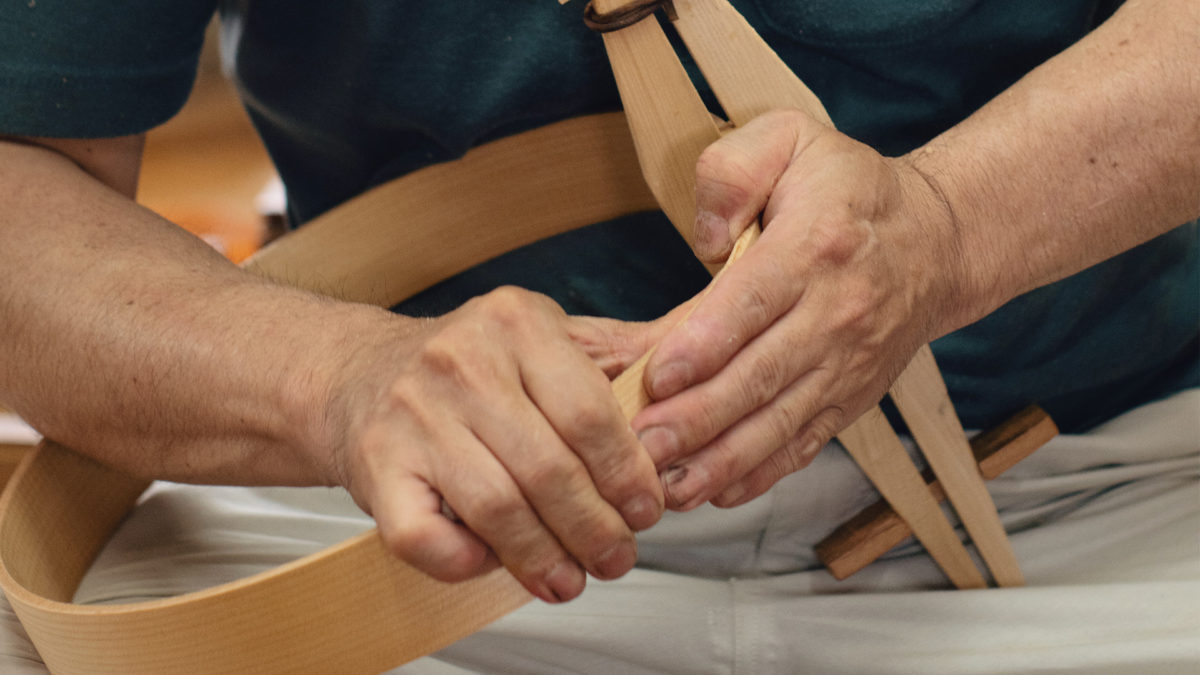
[Features and Use of Techniques]
As one might expect, kijishi are artisans well-acquainted with wood, but due to the nature of the “mage” techniques they deal with, magemonoshi in particular devote extremely close attention to wood grain.
Magemonoshi split the logs and cut the wood themselves. The advantages of the masameita used for mage are that they have a dense grain which reduces the risk of deformation, and they absorb little moisture. However, even if they have the same straight grain, there is a variety of shapes, so the artisan ultimately must determine if it can be used for mage by eye.
As proprietor of Kurata Mokkosho, one of only two woodworking shops specializing in magemonokiji in Wajima, the magemonoshi Mitsuru Kurata had this to say.
“You can’t understand the condition of the wood unless you see it with your own eyes. Once you’ve done that, you use the best parts for bending material. While a straight grain is typical of masameita, some wood with a curved grain can also be used for mage. Mage is a process of repeated deformation. Even if it looks like a clean circle, parts of it are warped. Therefore, it doesn’t stand out very much, or rather, you correct it so it doesn’t stand out. That is where skill comes in.”
The wood used for bending is between 4.5mm to just under 5mm thick, and wide pieces are thinned down with a plane on the inner surface to make it easier to bend.
“First, I check the flex of the wood. I keep an eye on this while I plane it, making sure there will be as little warping as possible when it is made into a circle. There are other techniques for making it resistant to warping or easier to bend. For example, there’s a technique called ryobari for imparting a curve to both the front and back of the wood. This makes the wood flexible and easy to bend, and it is easier to fix later.
The soaked piece of wood is quickly bent using a form. The right amount of wood oils is essential to bending it without breaking it. Although there are also different ways of soaking depending on the type of wood, it all makes sense when Kurata mentions that “There are methods of soaking in hot water, but that makes it easier for moisture to evaporate, and may draw out too much of the oils.”
“It may all comes under the single term of mage, but there are actually many different mage techniques, like hikimage (a method of scoring the inner surface of the piece to be bent with a saw) and uchimage (a method of cutting the edges to join multiple pieces together).
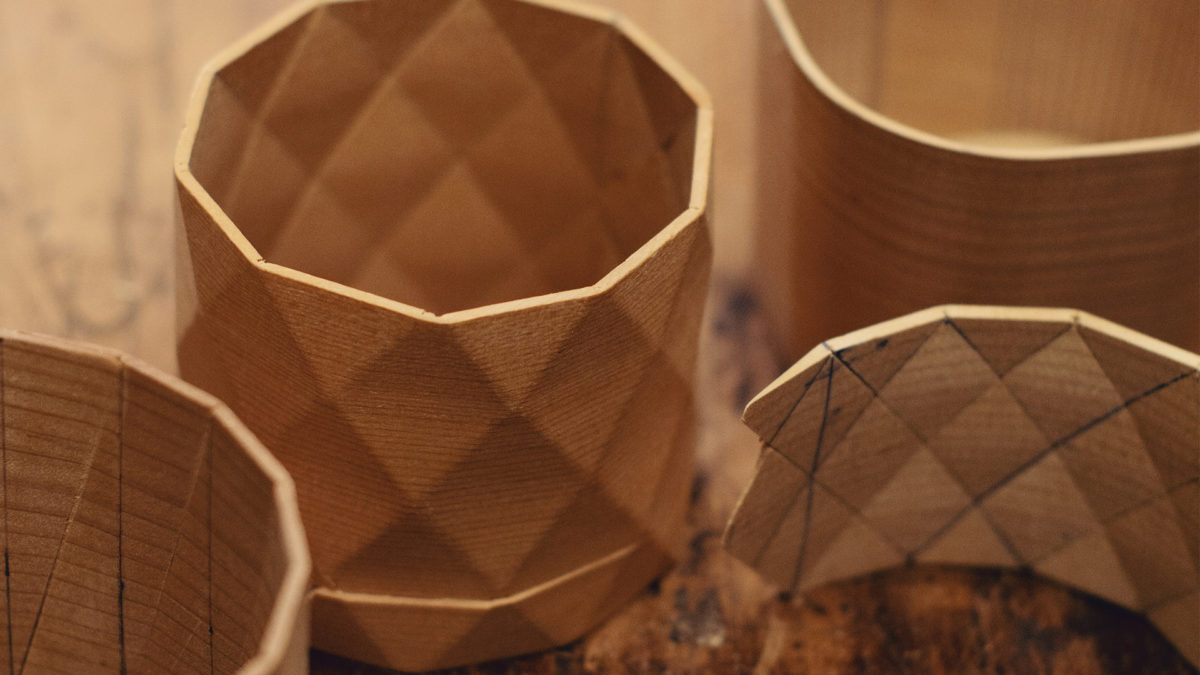
When asked, Kurata replies that in addition to semicircles, “I can also create more complicated shapes or designs” by using such techniques.
The fact that there are techniques for creating magemono in a wide range of shapes aside from the standard circles and oblongs open up vast possibilities for their application. At the same time, one might say that this suggests there exist no few “dormant techniques” not ordinarily used in the world of traditional handicrafts.