ARTICLES
Uwa-nuri (Top coat)
This is the final step of the lacquering process. High-quality lacquer of high purity (repeatedly filtered) is painstakingly applied. Dust and dirt are strictly kept away during the painting process, and no one other than the craftsmen is allowed to be present. Some craftsmen even work without clothes in case they have dust on them. It is a technique that requires delicacy, care, and above all, a high level of lacquering skill.
Process Overview
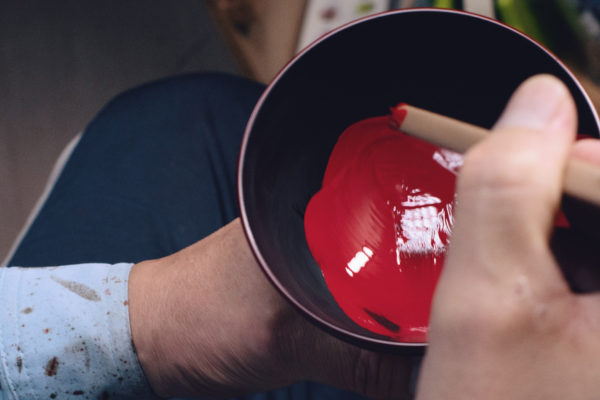
1 Uwa-nuri 1
After carefully removing dust and dirt from the surface of the medium-coated vessel with a brush or bird feather shaft, the lacquerer roughly coats the vessel with an appropriate amount of lacquer using a brush.
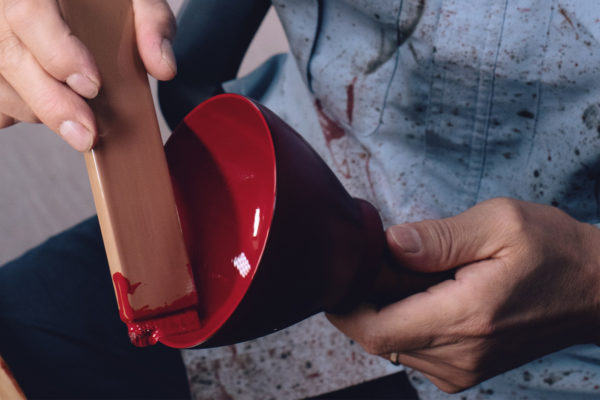
2 Uwa-nuri 2
Using a finishing brush, the lacquerer coats the lacquer to an appropriate thickness to avoid leaving an uneven surface. The lacquerer coats the inside and outside of the vessel separately.
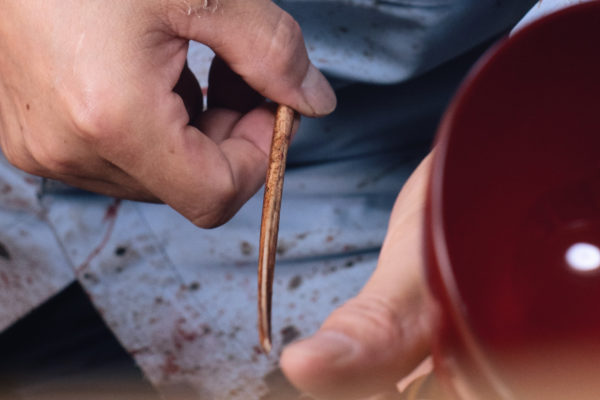
3 Fushi-age
The lacquerer removes dust from the surface of the lacquered vessel by using a picking stick or similar tool.
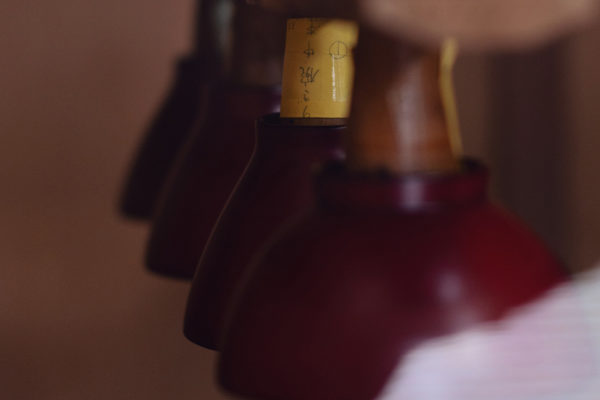
4 Drying
The lacquerer places the vessels in a lacquering bath that automatically rotates and periodically turns them to dry so that the lacquer does not drip and become uneven. When made into products without any coloring or decorations, vessels that have finished drying are called nuritate (literally, freshly-lacquered). If the vessel is to have decorative patterns, etc., the process continues to the next stage.
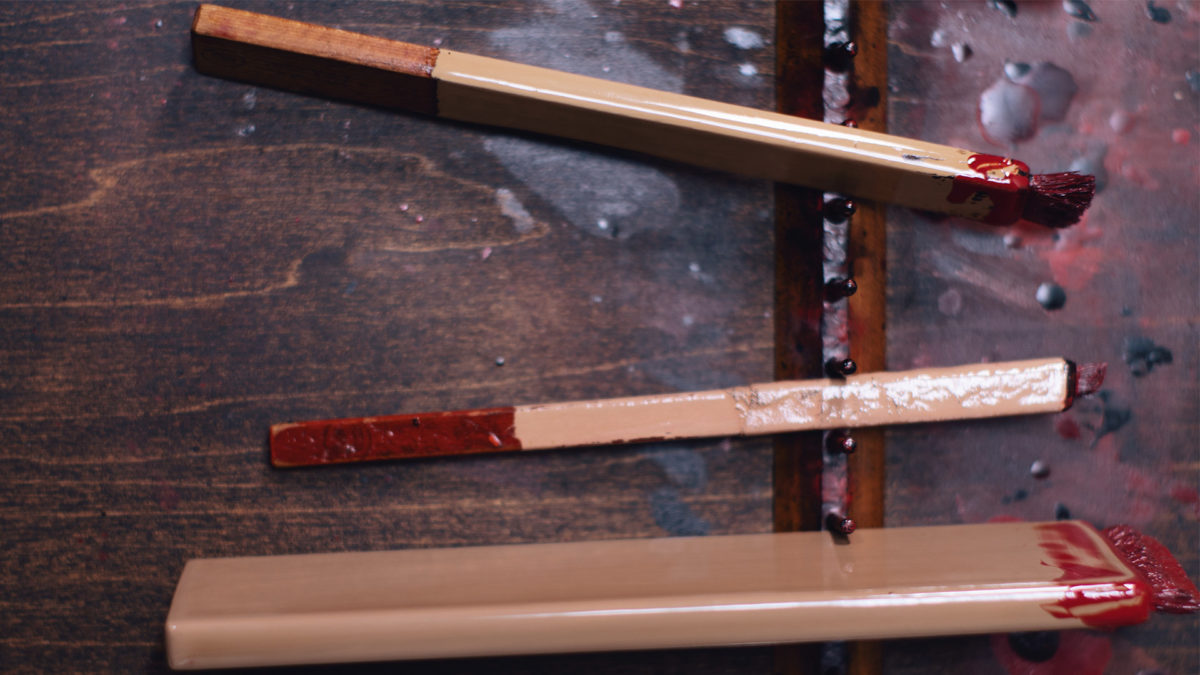
[Tools]
Brush, spatula, bird's feather shaft, picking stick (thin bamboo stick with pointed end), rotating bath, wet bath, etc.
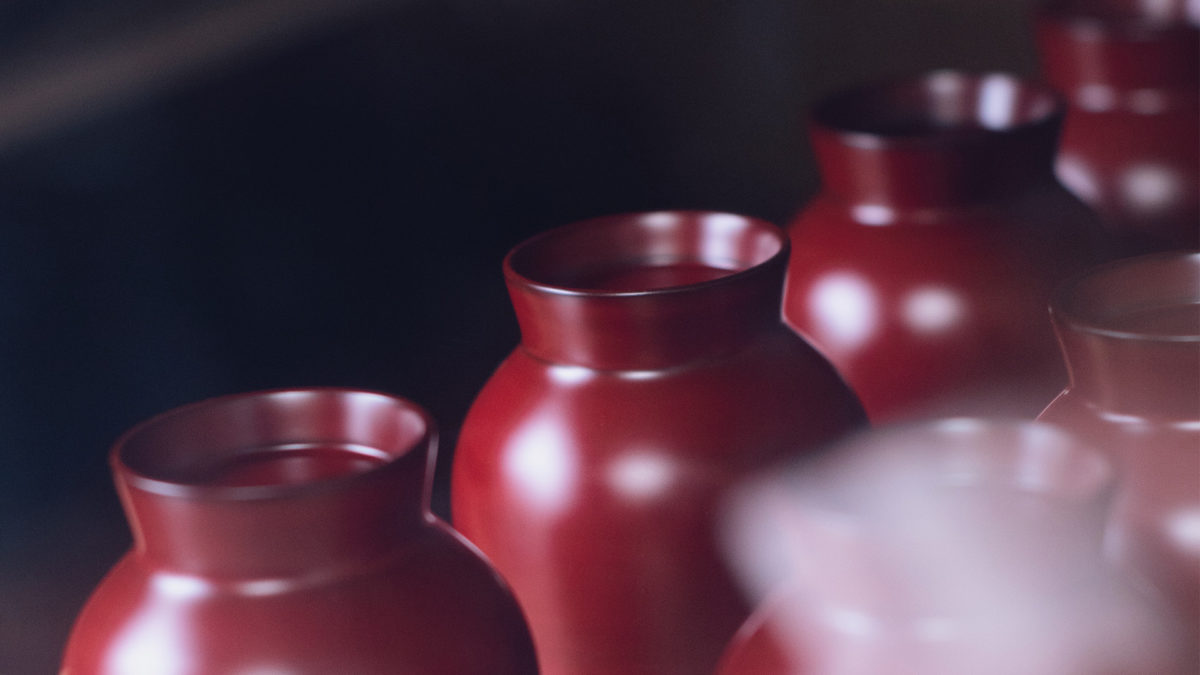
[Features and Use of Techniques]
Lacquer finishing broadly falls into two categories: nuritate and roiro.
The top coating process is a technique using the first type of finish, also known as hana-nuri (flower lacquering). Since the lacquerer does not polish the surface after the lacquering process, one can feel the inherent beauty of the lacquer material in this finish.
Tomio Sakashita, a lacquerer specializing in the top coat, talks about the lacquer used in this stage.
“Basically, we use colored lacquer, a mixture of pigment and shu-ai-urushi (* lacquer refined to a translucent candy color by removing water from raw lacquer), as the base of the color. The lacquerer is responsible for mixing the lacquer. The lacquer's condition and properties vary depending on its origin and the year/season it was collected, so it is fine-tuned each time according to its condition. This is why we say that lacquer is a living thing. In addition, since the lacquer changes with the temperature and humidity of the room, it is difficult to say in words or numbers what proportions are best to use. I would even say that I rely on my senses from experience, and I think if my senses tell me it's the best, then it's the best.”
The top coat is unique not only in the lacquer but also in the tools used.
“Unlike other processes, the top coat is applied with a brush made of human hair. This is because the strength of the human hair at its base and its softness are suitable for smoothly finishing the lacquer. This brush I am using now is made from a woman's hair. The types of brushes used vary in size and bristle length, according to what the lacquerer is most comfortable with.”
The lacquering process requires the utmost attention.
“The most important thing to keep in mind is ensuring that the brush does not leave any marks. It's also essential to keep the surface free of debris. The debris I'm referring to is tiny, like grains of sand, so no matter how careful I am, it can still get on the surface. So, each time I find them, I remove them and clean up the surface. I remove the debris with a thin, sharp shaft carved from a black kite feather with the hair plucked. Never use metal rods since they will scratch the coated surface.
Once coated, we dry the vessels in a specialized room with a rotating bath called a kaiten-buro.
“To prevent the lacquer from dripping down, we dry it by flipping it over every five or six minutes. In addition, how the lacquer dries depends greatly on temperature and humidity, so it's also essential to adjust for these factors. The lacquer will dry too quickly and shrink if it's too humid. If this happens, brush marks appear, the lacquer color becomes too dark, and the final product is ruined. As with the preparation of colored lacquer, the finished product is strongly affected by the weather, so it's a job that keeps me on my toes from start to finish.”
When asked, Sakashita-san stated that lacquer could be applied not only to wood but also to specially coated metals. In addition, there are many collectors in Japan and abroad of lacquered fountain pens and other products, and there is a certain amount of demand for them.
However, the first step in finding new ways to use lacquer is to consider what to apply it to, considering the advantages of lacquer, such as (1) resistance to acids and bases, (2) imperviousness to alcohol, petroleum, benzine, etc., (3) excellent moisture proofing and preservative properties, (4) imperviousness to electricity, etc. This may be a stepping stone to the second stage of application.