ARTICLES
Hou-kiji
This technique is for woodwork with complex shapes and many curved surfaces, such as cabriole legs, lipped bowls, Buddhist altar fittings, and spoons. Its name comes from its extensive use of magnolia wood, which has moderate hardness and workability, and it is also known as kurimono-kiji, from the carving technique employed. Other typical items include flower stands, low tables, spouts for sake pots, and shelves.
Process Overview
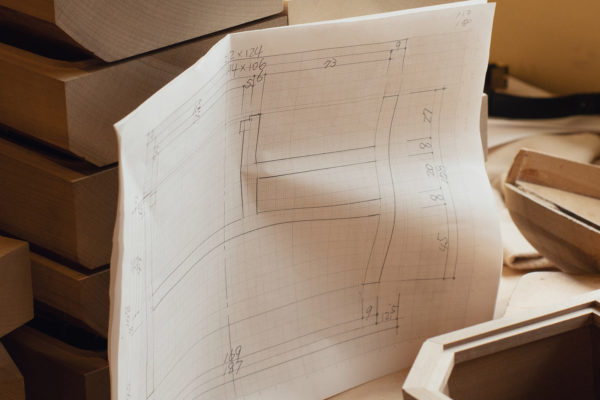
1 Drying
The logs are cut into boards based on the dimensions of the desired product and naturally dried outdoors in full sun and ventilation for at least six months, and then indoors for several months. After drying, the woodworker outlines each part of the final product (katachi-dori) and cuts each piece out according to the outlines (ki-dori).
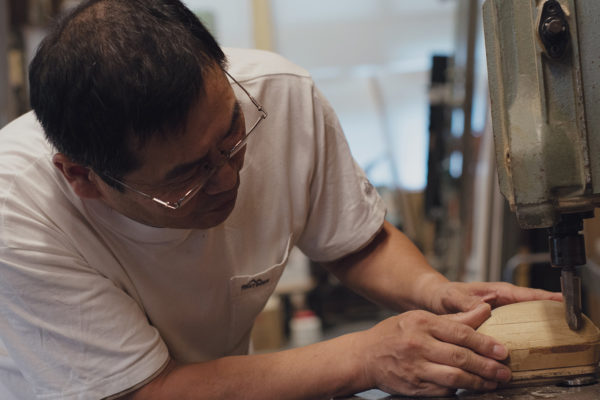
2 Medium-finish (carving)
After roughly carving each part using a power planer or a flat plane (a process called ara-kezuri), the woodworker carves out the overall shape according to the outlines using a chisel, craft knife, and kanna (Japanese plane) to create the rough shape.
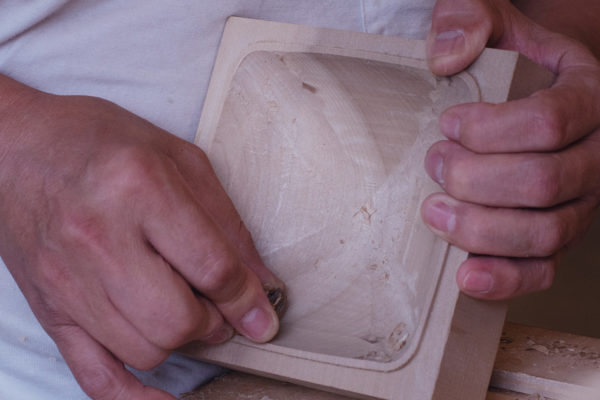
3 Finish (carving)
The woodworker uses a chisel, craft knife, and plane to carve out the rough mold's fine details (curved surfaces and other intricate parts) and finishes it into the shape according to the outline.
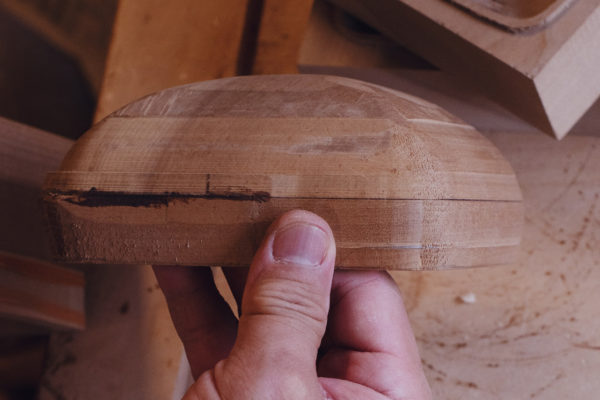
4 Rough finish
Using a craft knife and a plane, the woodworker smooths the surface of the wood and then polishes the entire surface with fine sandpaper.
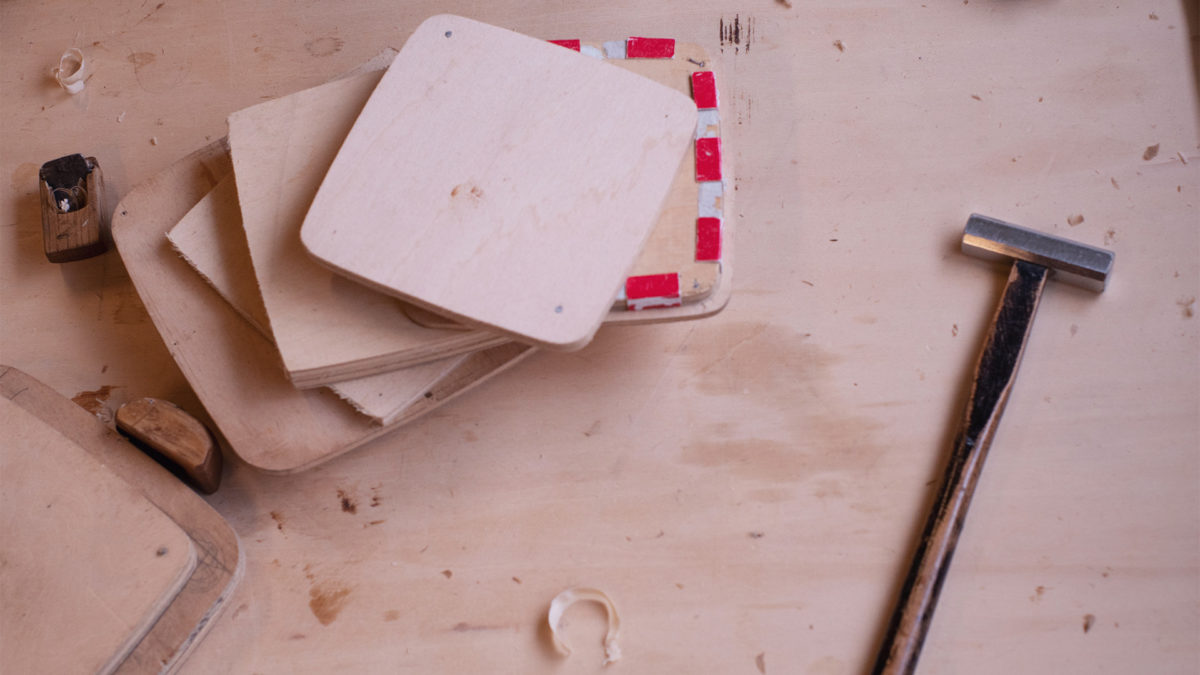
[Tools]
Saws, planes, miniature planes, chisels, craft knives, pincers, molds, etc.
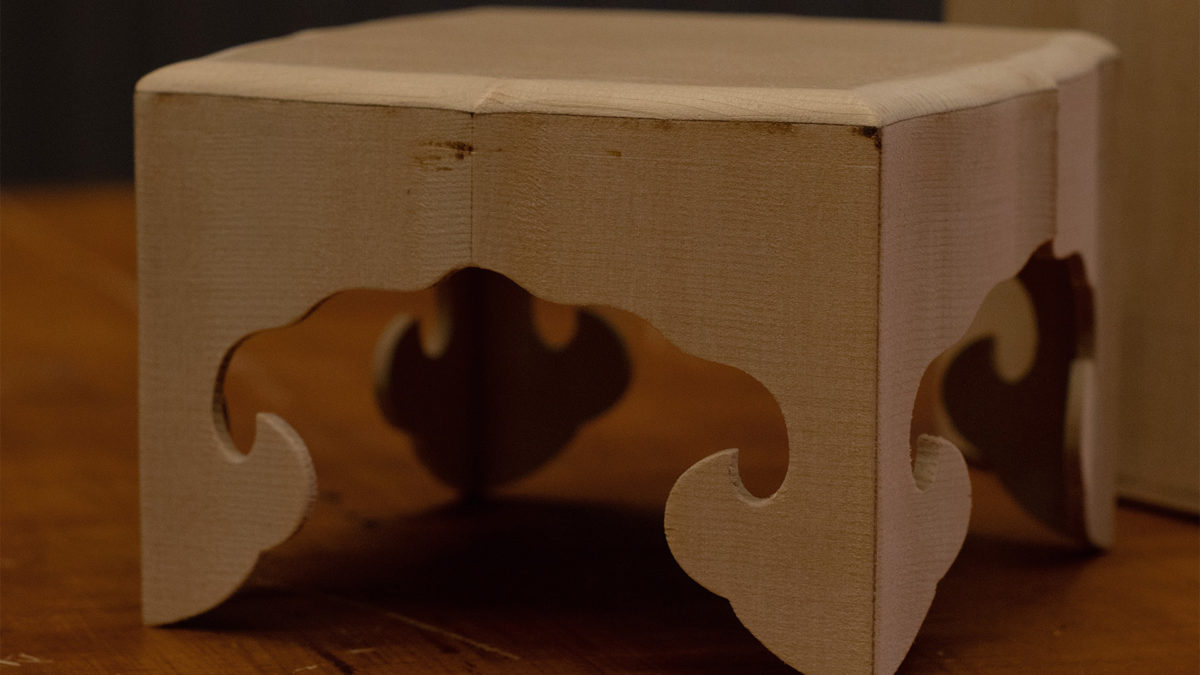
[Features and Use of Techniques]
"Versatility is a must. A woodworker must be able to carve out almost anything, from a large table to a small spoon. Hou-kiji is a technique for making all of that."
Kazunori Sumi, who oversees wood carving at Wajima Kirimoto, describes the Hou-kiji technique in his own words. Naturally, the tools used are also diverse, and Sumi-san's workshop has nearly 300 tools, such as miniature planes, namazori (a carving blade similar to that of a naginata), yariganna (has a long handle with a blade similar to the tip of a spear), and round chisels. Sumi-san reflects that his arsenal "naturally got bigger and bigger, just out of necessity."
“A sake pot, shaped like a kyusu (teapot), holds toso (sake) for celebrations and other occasions. The woodworker specializing in bowls makes the round part of the body, and the woodworker specializing in Hou-kiji makes the spout. The curved surface of the spout needs to be carved to make it completely adhere to the body, which requires very delicate work. Needless to say, if sake leaks out when you fill the pot, we can’t sell it. Also, even a tiny gap will let moisture seep in, eventually causing severe cracks down the road.”
Many wooden products use Hou-kiji, such as jinbako, used to store incense wood (wood that emits aroma such as agarwood and white alder), cabriole legs, Buddhist altar fittings, and spoons. Naturally, the tools used are also diverse, and Sumi-san's workshop has nearly 300 tools, such as miniature planes, namazori (a carving blade similar to that of a naginata), yariganna (has a long handle with a blade similar to the tip of a spear), and round chisels. Sumi-san reflects that his collection of tools "naturally got larger and larger, simply out of necessity." In addition to these, jigs (a generic term for tools used to direct and guide the working position of parts and tools during processing and assembly) are essential for Hou-kiji woodworkers and woodworkers in general, says Sumi-san.
“Making jigs with your own hands is the first step in becoming a Hou-kiji woodworker. For example, anyone could make a single spoon if they could spend dozens of hours on it. Instead, we need to think about how we can save time and make things more efficient and what kind of jigs we need, or we won't be able to do this job. Making a jig requires a certain amount of experience, and it is not something you can do quickly and easily, but it is essential to learn to think for yourself and assemble it as a first step. In that sense, when you make something, it's your job to figure out how to make it."
Mr. Sumi, who is passionate about the importance of jigs, has something he wants to create.
“It would be interesting to make a western-style version of a palatial low table with cabriole legs. Making the legs longer inevitably makes the table unstable, but it's my job to find a technical workaround. I'm just speculating, but I think that the legs would have to be removable. Well, I can't say for sure since I haven't worked on it yet, but I think we'll need special jigs for that.”
Adapting Japanese designs to Western items is another use of the Hou-kiji technique. The obstacles that stand in the way may lead to new techniques and even more uses.