ARTICLES
Togimono (Polishing)
This is the process of leveling the uneven surface left behind by the coating for a more beautiful finish. Polishing also creates microscopic scratches, where the lacquer seeps in, enhancing the adhesion between the wood and the lacquer. The grinding stones used can be round, sharp, or concave, depending on the shape of the polishing surface.
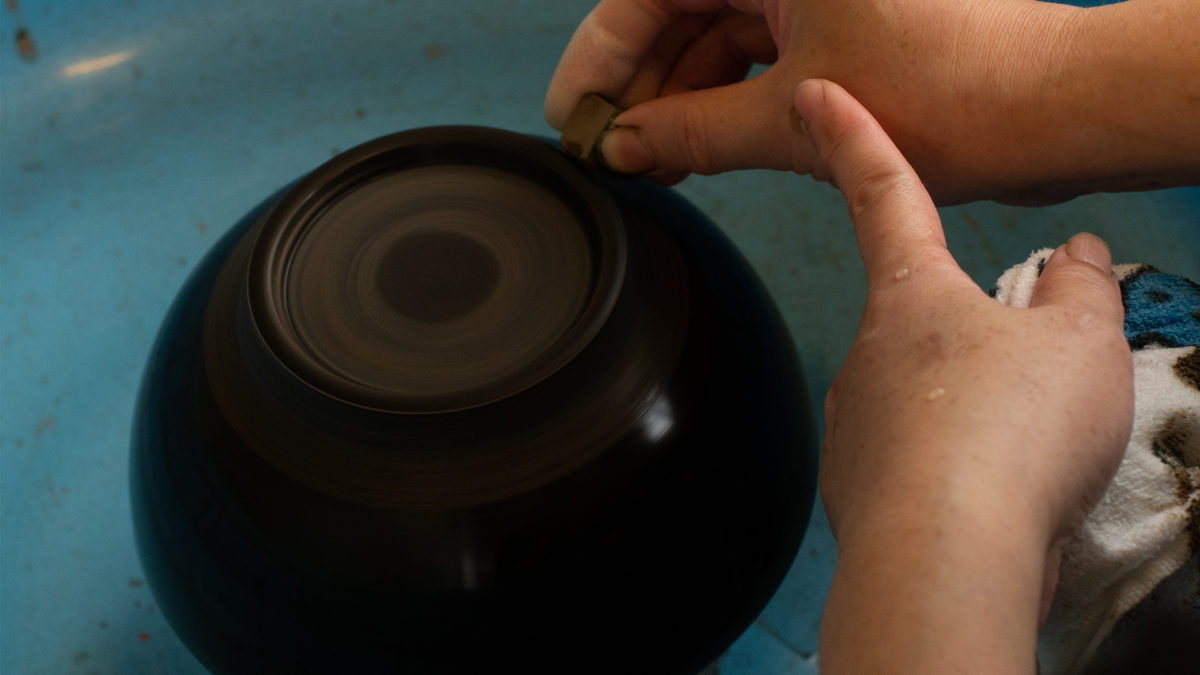
[Process / Distinctive Techniques]
Ji-togi: This is a technique for smoothing the surface of a vessel, after undercoating and smoothing with water, to shape the vessel according to its final dimensions. The final stage of the undercoating process, this step is so important that it is not an exaggeration to say that the quality of the polish determines the quality of the finished lacquerware. Excellent molding skills are required to polish the vessel to produce beautiful straight lines, curves, and flat surfaces, while adjusting the corners and the subtle changes in thickness at the edges. Square pieces (such as stacked boxes) are polished by hand, while Turnery (such as bowls) are polished using a grinding wheel.
[Tools]
Grinding stone, awasedo (small piece of slate stone used to smooth out the unevenness of the grinding stone and remove oil from the stone), sandpaper, grinding wheel, etc.
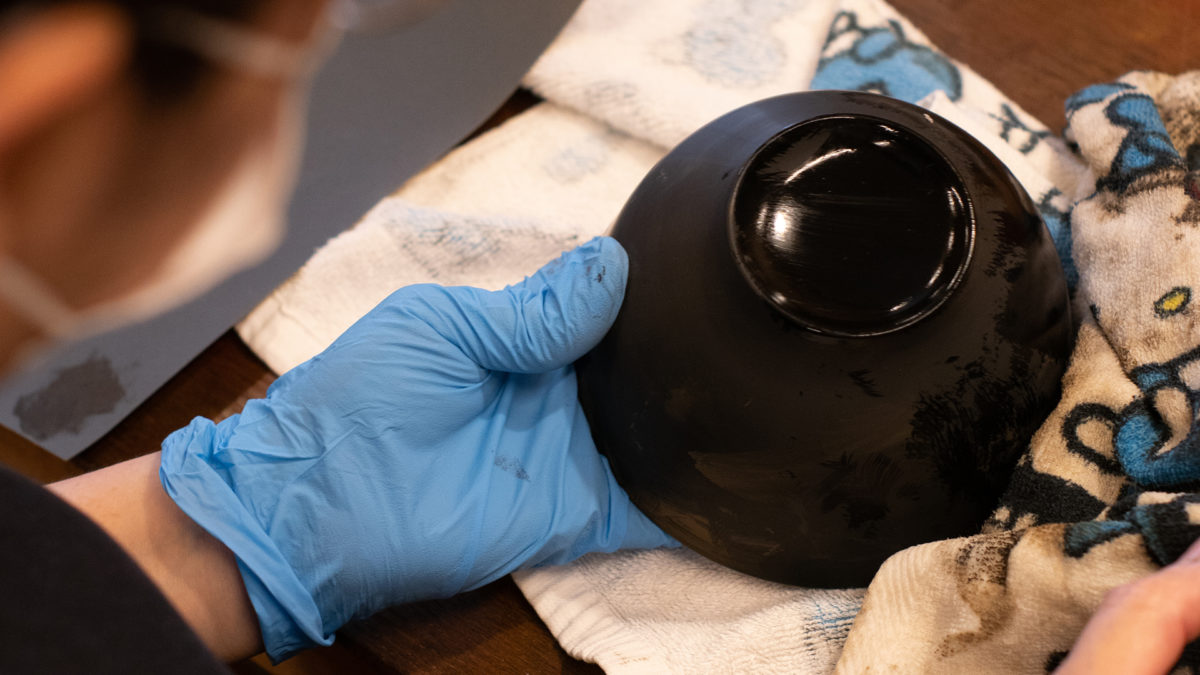
[Features and Use of Techniques]
At first glance, the polishing process may seem like a simple chore, but it plays several essential roles indispensable when making lacquerware. So what exactly goes into the polishing process?
Shizue Sakashita, who oversees polishing products at Wajima Kirimoto, tells us.
“The first step is to find the elevated (thicker) areas of the coating and polish those uneven surfaces. It is a process of polishing the high parts to match the low parts. We use the grinding stone to find the surface's uneven parts and then polish the surface based on how it feels in our hands and the wood's reflection in the light. Lacquer has the characteristic of pulling together when it hardens, so it becomes thinner on the interior of the surface and thicker around the edges. We find the subtle differences in elevation and polish them to make the entire surface uniform.”
The evenly finished surface is then coated again with lacquer. During this process, the lacquer adheres to the surface by penetrating the scratches (grooves) made by the grinding process.
“The polishing process not only creates a beautiful lacquered surface but also strengthens the lacquerware. Polishing also plays an essential role in giving the vessel its shape. In addition, polishing the lacquered surface and examining the surface reveals any defects, such as minute pores or chipped edges. If there is some defect, we reverse the process to the point where we can repair the fault. This is why the polishing process immediately before the middle coat and top coat, ji-togi, is particularly essential. It also serves as the last inspection to determine if the surface is perfectly coated.”
The process of polishing is indeed a behind-the-scenes effort. Still, in terms of its potential, it would be interesting to have products that reveal this process, in which the polishing marks appear deliberately on the surface. Another technique that focuses on polishing is roiro, which comes in during the decoration process, and uniquely enhances the lacquerware's potential.
Naka-nuri (Middle coat)
This process completes a beautiful foundation for the top coat. First, the lacquerer coats the entire surface with a special lacquer for the medium coat, which is purer than the undercoat's lacquer, using a brush. The lacquer is then dried in a nushi-buro (container made of cedar planks) while controlling the temperature and humidity The lacquerer then polishes the surface with a plane to remove dust and debris (sabi-zarai), fills dents and other defects with lacquer (tsukuroi-sabi), and polishes the surface with a blue whetstone or Suruga charcoal (wuki-age) before passing it on to the top coating process.